Leading the Future of Manufacturing: The Role of Plastic Mold Makers in Advanced Industries
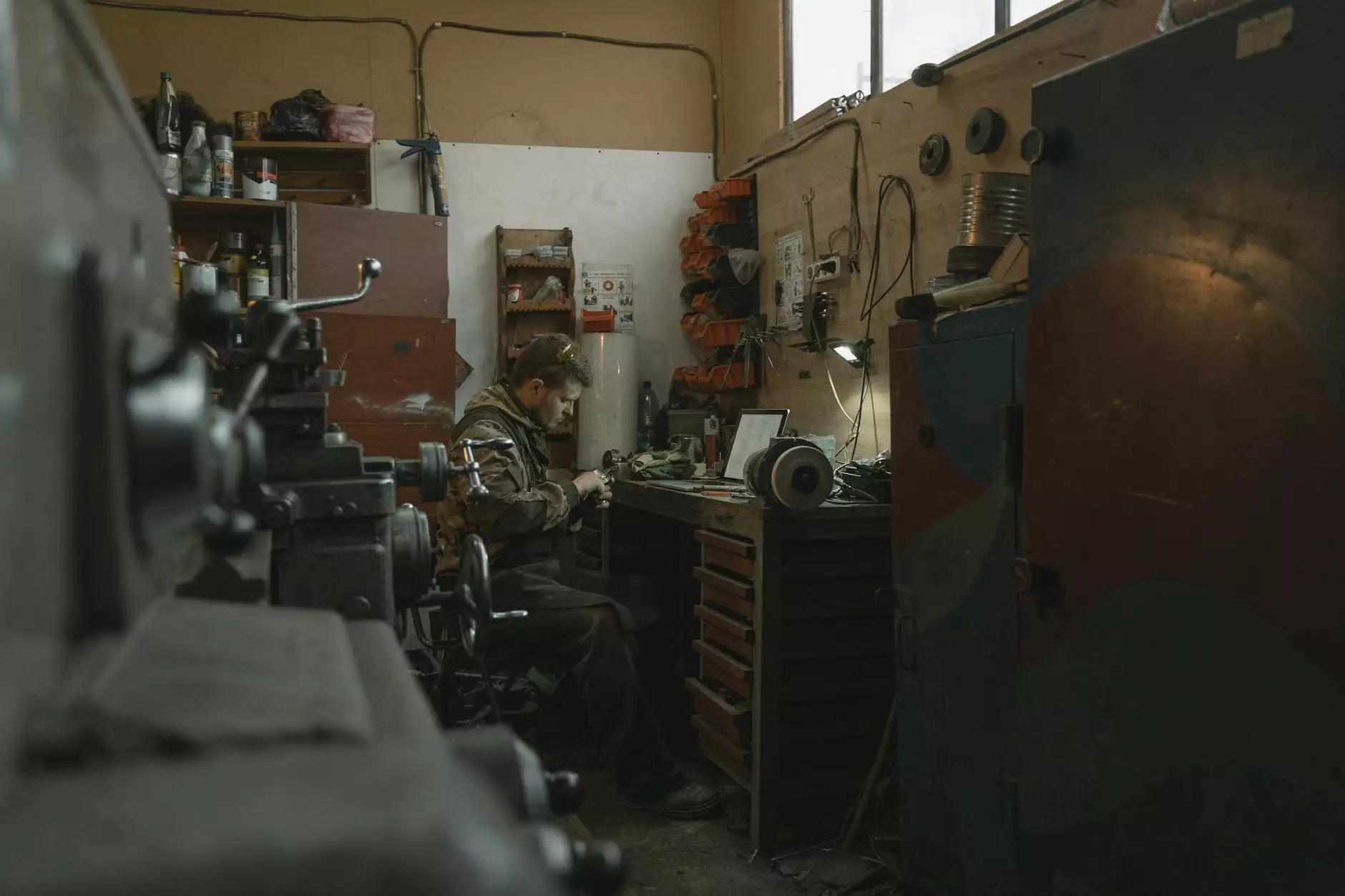
In the rapidly evolving landscape of manufacturing, the importance of precision, innovation, and high-quality craftsmanship cannot be overstated. Plastic mold makers and metal fabricators are at the forefront of this revolution, providing essential components and custom solutions that power everything from consumer electronics to automotive parts. At deepmould.net, we pride ourselves on delivering exceptional manufacturing excellence, leveraging cutting-edge technology and decades of industry experience. This comprehensive guide explores how plastic mold makers are shaping the future of manufacturing and why partnering with a professional and skilled metal fabricator is crucial for your business success.
The Critical Role of Plastic Mold Makers in Modern Manufacturing
Plastic mold makers are the architects behind precision-engineered molds that enable the mass production of complex plastic parts. Their expertise ranges from conceptual design to manufacturing, ensuring every product meets stringent quality standards. The importance of these mold makers extends across multiple industries, including automotive, consumer goods, medical devices, and electronics.
Key Responsibilities of Top-tier Plastic Mold Makers
- Design Optimization: Utilizing advanced CAD software to create efficient, durable molds that optimize manufacturing processes.
- Material Selection: Choosing the right mold materials such as aluminum or steel, depending on production volume, part complexity, and durability requirements.
- Precision Machining: Employing CNC machining, EDM, and other high-precision techniques to craft molds with micrometer accuracy.
- Prototyping and Testing: Developing prototypes to verify mold design functionality, ensuring seamless production runs.
- Lifecycle Management: Providing maintenance, repair, and modification services to extend mold longevity and optimize performance.
Innovations Driving Excellence in Plastic Mold Making
Emerging technologies are revolutionizing the plastic mold makers industry, enabling faster turnaround, enhanced precision, and cost reduction. Key innovations include:
Computer-Aided Design (CAD) & Computer-Aided Manufacturing (CAM)
These digital tools allow geometric precision and simulation before actual mold production begins. This reduces errors, shortens lead times, and improves the overall quality of the molds.
Rapid Prototyping & 3D Printing
Integrating 3D printing into the mold development process helps in creating accurate prototypes for testing, which expedites the feedback cycle and refines final designs.
Advanced Materials & Surface Treatments
Modern materials such as high-performance steels and aluminum alloys, combined with innovative surface treatments, improve mold durability and release properties, leading to better product quality and extended mold life.
Why Metal Fabricators Are the Backbone of Quality Manufacturing
Metal fabricators play an essential role in creating the structural backbone of molds, fixtures, and custom components. Their craft extends beyond basic fabrication to include innovative solutions tailored to client needs, ensuring that every piece is not only functional but also optimized for performance.
Core Services Offered by Skilled Metal Fabricators
- Cutting and Bending: Precision laser cutting, plasma cutting, and bending of metals such as steel, aluminum, and copper to exact specifications.
- Welding and Assembly: High-quality welding techniques including TIG, MIG, and spot welding to assemble complex parts reliably.
- Surface Finishing: Powder coating, anodizing, and polishing to improve aesthetic appeal and corrosion resistance.
- Custom Fabrication: One-off prototypes and large-scale production, including custom fixtures, support frames, and tool modifications.
The Synergy of Plastic Mold Makers and Metal Fabricators: Building Superior Manufacturing Solutions
The collaboration between expert plastic mold makers and metal fabricators leads to innovative, high-performance manufacturing solutions. Together, they provide integrated services that span the entire product development lifecycle, from initial concept to mass production.
Advantages of this Collaborative Approach
- Enhanced Precision: Combining advanced mold design with precisely fabricated metal components ensures tight tolerances and consistent quality.
- Reduced Lead Times: Streamlined workflows between design and fabrication minimize delays and accelerate time-to-market.
- Cost Efficiency: Optimized manufacturing processes and durable, high-quality molds reduce waste and rework, saving costs in the long term.
- Innovation & Customization: Custom solutions tailored to specific project requirements improve product performance and market competitiveness.
Choosing the Right Partner: How DeepMould.net Sets Industry Standards
As industry leaders, deepmould.net offers unmatched expertise in both plastic mold making and metal fabrication. Our comprehensive services are designed to meet the diverse needs of our clients, ensuring high precision and quality at every stage.
Our Commitment to Excellence
- Own Modern Equipment: We utilize state-of-the-art CNC machines, EDM, and surface treatment facilities to maintain the highest standards.
- Experienced Workforce: Our team comprises industry-certified engineers, machinists, and craftspeople dedicated to precision craftsmanship.
- Quality Assurance: Rigorous testing protocols and inspection procedures guarantee that all molds and fabricated components meet or exceed industry standards.
- Customer-Centric Approach: We prioritize client communication and collaboration to develop tailored solutions that perfectly match project goals.
Industries Benefiting from Our Services
Our expertise as plastic mold makers and metal fabricators supports a broad range of industries, including:
- Automotive: Manufacturing precision molds for interior and exterior parts, ensuring durability and aesthetic excellence.
- Electronics & Appliances: Creating complex plastic components and custom metal housings for devices and home appliances.
- Medical Devices: Producing sterile, high-precision molds and fabrications for life-saving medical equipment.
- Consumer Goods: Developing innovative designs for packaging, household items, and personal care products.
- Industrial Equipment: Fabricating robust metal frames, supports, and molds to withstand harsh operational environments.
The Future of Manufacturing: Embracing Innovation and Sustainability
The industry is moving toward sustainable practices and smart manufacturing, emphasizing eco-friendly materials, waste reduction, and energy-efficient processes. At deepmould.net, we are committed to innovation that aligns with environmental responsibility while maintaining the highest quality standards.
Implementing Green Manufacturing Practices
- Utilizing recyclable materials in mold components and fabrication processes.
- Adopting energy-efficient machinery and automation to reduce power consumption.
- Reducing waste through precise CAD design and process optimization.
- Implementing closed-loop systems for material reuse and recycling.
Conclusion: Partnering for Unmatched Success in Manufacturing
Whether you're developing a new product or optimizing existing manufacturing processes, partnering with plastic mold makers and metal fabricators specializing in high-quality craftsmanship is vital for success. At deepmould.net, we combine innovation, experience, and commitment to deliver solutions that elevate your business. Our integrated approach ensures that your vision becomes reality with precision and efficiency, setting new standards in the industry.
Invest in expertise. Choose quality. Trust the leaders. Let deepmould.net help you achieve manufacturing excellence today and into the future.