Understanding the Silicone Membrane for Vacuum Press Applications
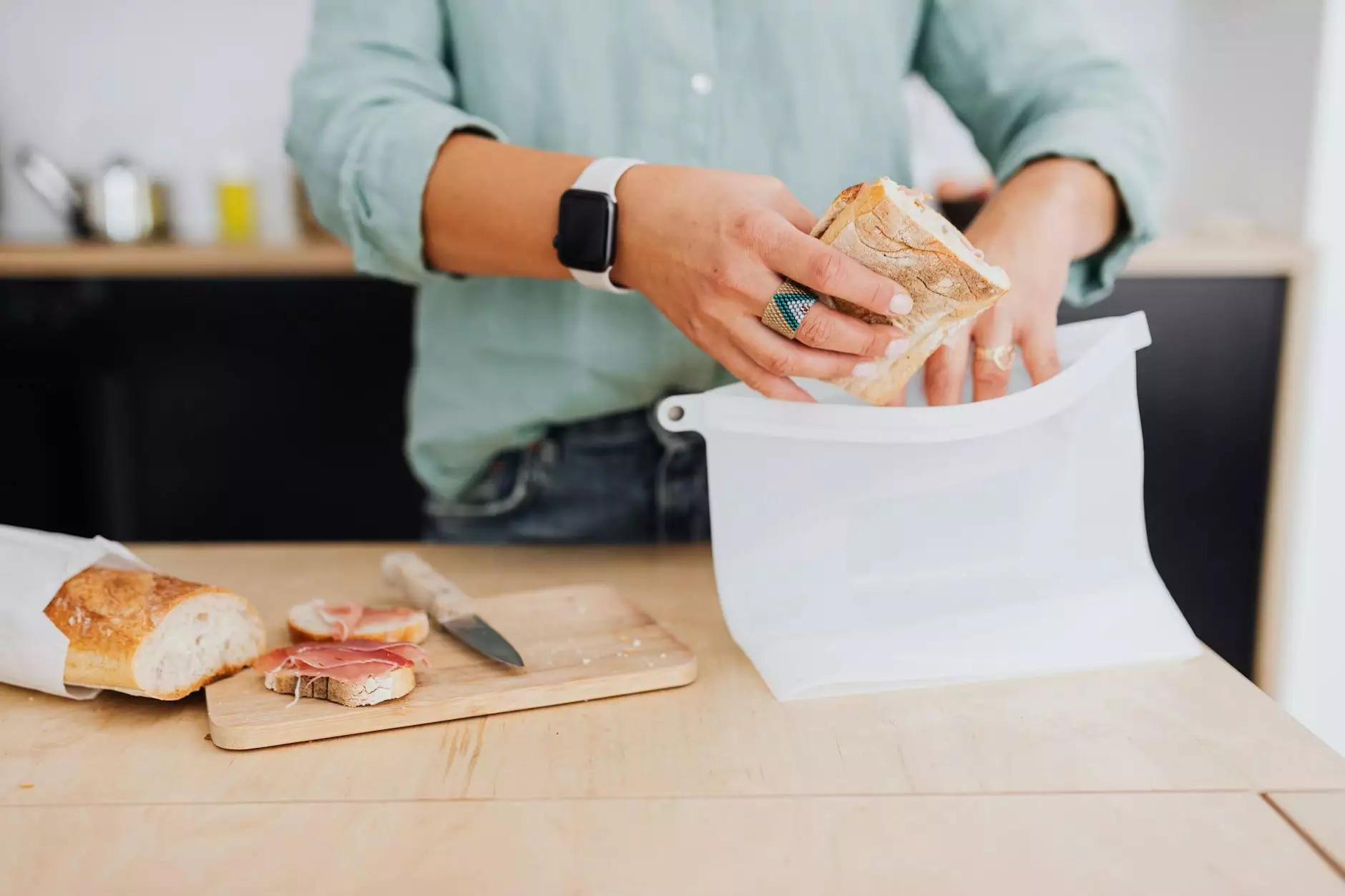
In the world of vacuum presses, the quality and functionality of the components play a significant role in ensuring successful operations. One of the most critical components is the silicone membrane for vacuum press. This article elaborates on what silicone membranes are, their importance, types, benefits, and how to choose the right one for your needs.
What is a Silicone Membrane?
A silicone membrane is a flexible, high-performance elastomer designed to create a reliable seal during the vacuum pressing process. These membranes are primarily used in industries such as woodworking, automotive, and aerospace, where precision and durability are paramount. Unlike traditional materials, silicone membranes offer superior flexibility and resilience, making them ideal for various applications.
The Importance of Silicone Membranes in Vacuum Pressing
Silicone membranes provide a multitude of benefits that enhance the efficiency of vacuum presses:
- Durability: Silicone is resistant to heat, cold, and a range of chemicals, ensuring a longer lifespan and consistent performance.
- Flexibility: The flexibility of silicone membranes allows them to conform to various shapes and surfaces, making them suitable for a wide array of applications.
- Temperature Resistance: Silicone membranes maintain their integrity under high and low temperatures, making them perfect for industrial applications.
- Ease of Use: They are easy to install and replace, minimizing downtime and maintenance efforts.
- Excellent Sealing Capability: The superior sealing capacity ensures effective vacuum creation, leading to better results in pressing.
Types of Silicone Membranes
When searching for a silicone membrane for vacuum press, it's essential to understand the different types available on the market:
1. Smooth Surface Membranes
Smooth surface silicone membranes are perfect for applications that require a consistent contact area. Their uniform surface helps distribute pressure evenly and achieves a clean finish.
2. Textured Surface Membranes
Textured surface membranes create a better grip on the materials being pressed. This texture can help keep components in place during the vacuum process, leading to greater accuracy and better results.
3. Natural Rubber Membranes
While not silicone, natural rubber membranes can also play a role in vacuum pressing. They offer elasticity and strength, though they may not withstand high temperatures as well as silicone.
Key Applications of Silicone Membranes in Industries
Silicone membranes are not limited to just one industry; they have a wide array of applications:
- Woodworking: Used to press veneered surfaces and create laminated materials.
- Aerospace: Essential for forming composite materials in fuselage and wing construction.
- Automotive: Utilized in pressing automotive panels, ensuring perfect fits and finishes.
- Medical: Employed in creating components that need precise shape and integrity for medical devices.
Benefits of Using Silicone Membranes for Vacuum Pressing
The adoption of silicone membranes in vacuum pressing brings numerous advantages:
- Quality Assurance: Achieving high-quality results with minimal defects is vital, and silicone membranes provide that reliability.
- Cost-Effectiveness: Although the initial investment may be higher than other materials, their long life and reduced downtime can lead to lower overall costs.
- Environmental Resistance: Silicone is an eco-friendly substance, resistant to UV light, ozone, and moisture.
- Versatility: These membranes can be used across various temperature ranges, making them adaptable to multiple settings.
How to Choose the Right Silicone Membrane
When selecting a silicone membrane for your vacuum press, consider the following factors:
- Thickness: Depending on your application, choose a thickness that provides the right balance between flexibility and durability.
- Surface Texture: Decide if a smooth or textured finish is more appropriate based on the materials you will be working with.
- Temperature Rating: Ensure the silicone membrane can withstand the temperatures it will be exposed to during pressing.
- Compatibility: Check if the membrane is compatible with the specific adhesives or materials in use to avoid chemical reactions.
Maintenance Tips for Silicone Membranes
To maximize the lifespan of your silicone membranes, follow these maintenance tips:
- Regular Cleaning: Use a mild detergent and water to clean the membranes after each use, avoiding abrasive cleaners that can damage the surface.
- Inspect for Damage: Regularly check for cracks, tears, or deformation to ensure optimum performance.
- Proper Storage: Store membranes flat in a cool, dry place to prevent bending or creasing.
- Avoid Extreme Temperatures: Do not expose the silicone membranes to extreme heat or cold when not in use.
Conclusion: Invest in Quality Silicone Membranes
In conclusion, the use of a silicone membrane for vacuum press applications is an investment that pays off in reliability and performance. Understanding the types, applications, and benefits will empower you to make informed choices that enhance your business outcomes. Consider exploring options at vacuum-presses.com, where you can find a wide range of membranes and vacuum system parts tailored for your needs.
By investing in high-quality silicone membranes, you not only improve your processing capabilities but also ensure a higher standard of production quality, which is essential in today's competitive market. Make the switch to silicone today and experience the difference it can make in your vacuum pressing applications!